Generator Plant Delivery
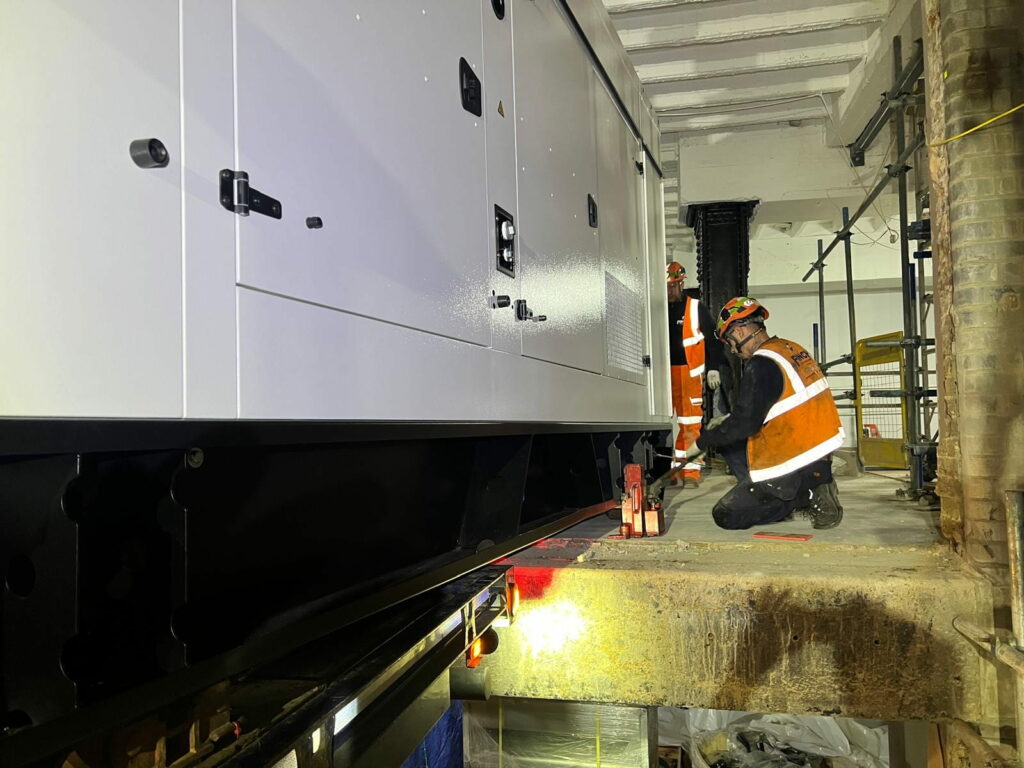
Generator Plant Delivery
Not all projects require a massive amount of specialist equipment; instead, they often demand skilled professionals who know how to get into tight, challenging spaces. In this case, it was our expertise at Finch of Bookham, recently put to the test, combined with precise handling, that ensured the successful execution of the task, even in such confined conditions.
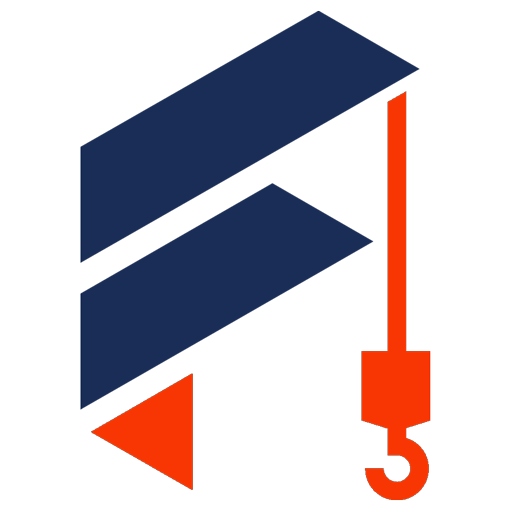
Initial Positioning and Preparation
A lorry loader vehicle, carrying a fuel tank and generator, reversed into the site then reversed up to the pre-formed aperture, positioned 1500mm from the loading bay level. Using its integral hydraulic rams and packing timbers, the vehicle bed was levelled against the floor of the Generator Room
Once levelled, a 6mm aluminium plate was laid across the threshold, bridging the gap between the vehicle and the Generator Room. The load was jacked up, and machine skates were placed beneath it.
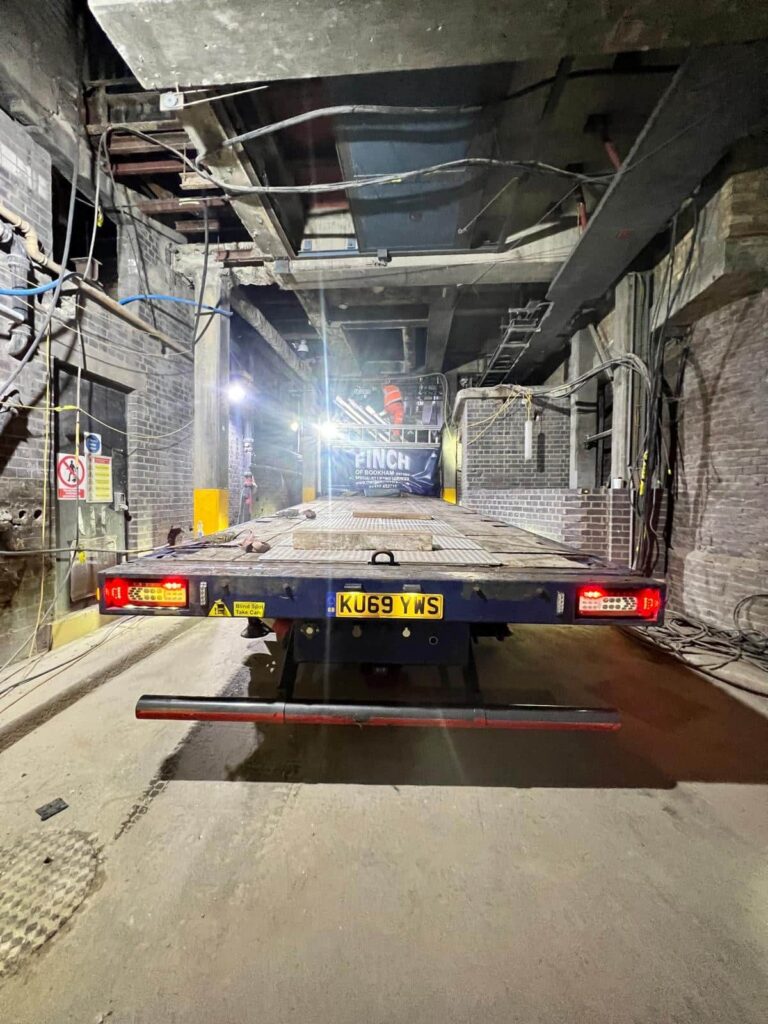
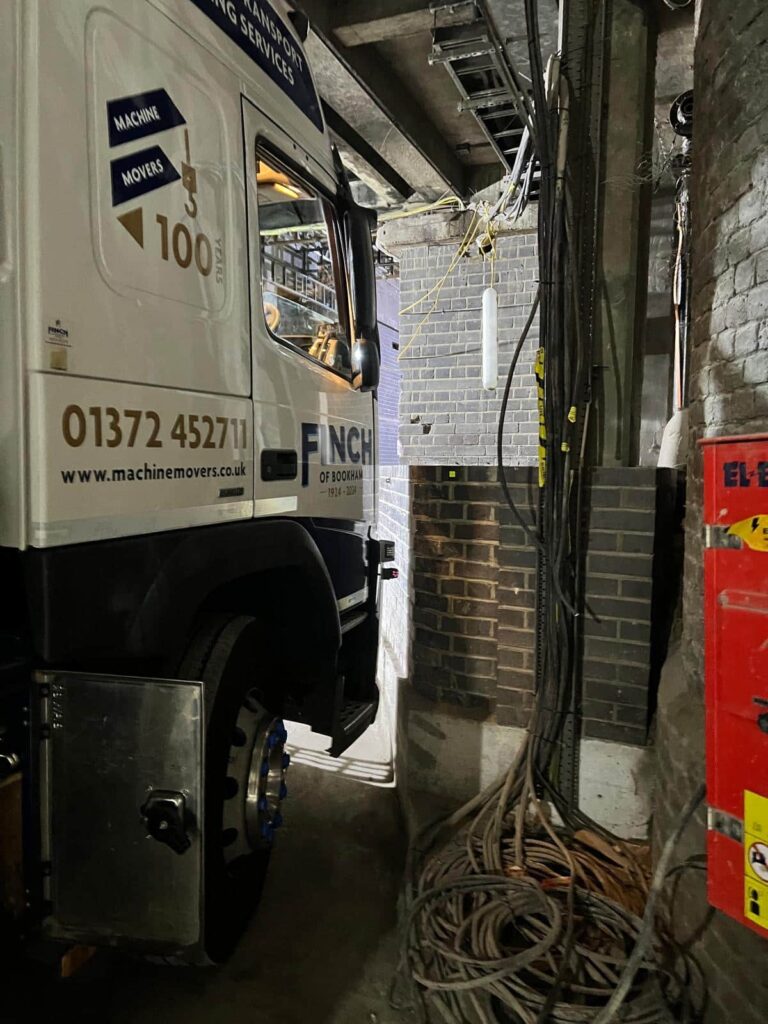
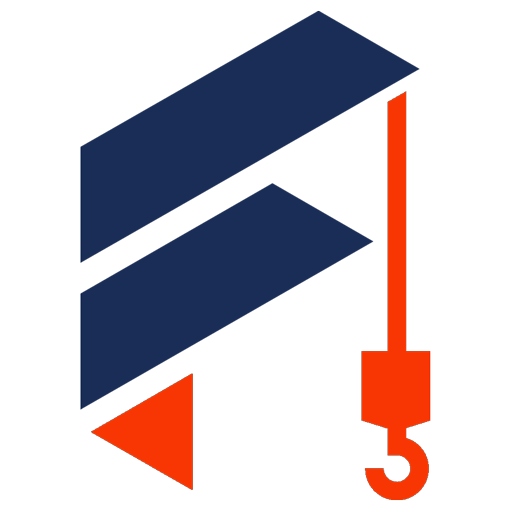
Load Transfer into the Generator Plant Room
A 2000kg nylon sling was passed around strategically placed columns within the Generator Plant Room. A Tirfor winch was then attached to the nylon sling, and the load was pulled from the vehicle, through the wall, and into the Generator Plant Room.
The load was positioned in a location and once in place, the load was jacked up again, the skates were removed, and the load was lowered to the ground.
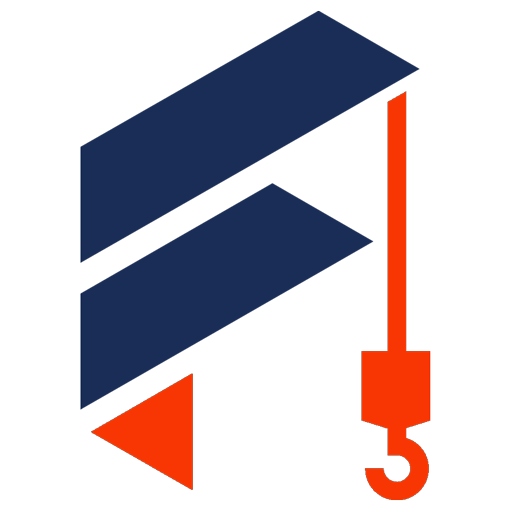
Forklift Operation and Remote Radiator Installation
Next, a forklift delivery vehicle, carrying a 2.5t forklift truck and a remote radiator, reversed into the site. Ramps were attached to the rear of the vehicle, allowing the forklift truck to drive off.
The remote radiator was offloaded with the forklift and driven to the designated area where it needed to be suspended. The forklift lifted the load under the direction of the mechanical fitter, who secured the remote radiator in place. On the mechanical fitter’s instruction, the forklift’s forks were lowered, leaving the radiator suspended at a high level.
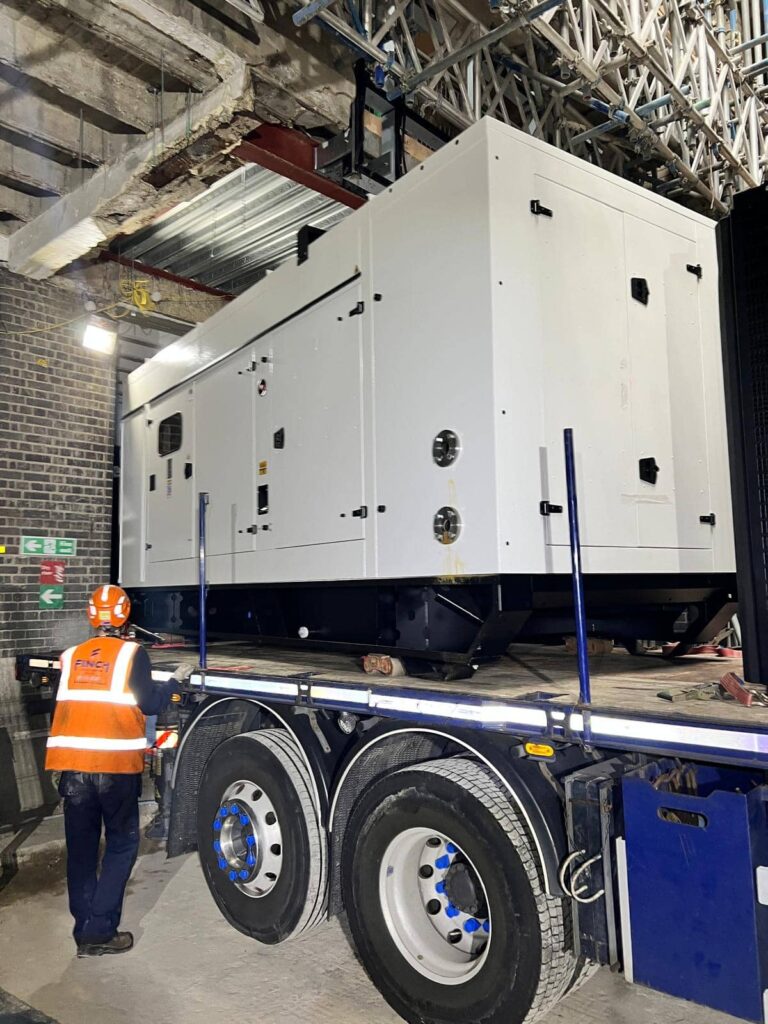